Thales – ERP Alliance Consultancy Case Study
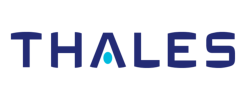
Name: Thales
Sector: Revenue Collection Systems
Location: Paris, France, and Copenhagen, Denmark
Following a change in operational leadership at the client, we managed a 6-month project to ensure the client was exploiting the system and getting maximum value from it. Management were concerned that different departments used to provide their own KPIs and reports, that often contradicted each other, they wanted a single database and set of reports that were agreed and approved by all.
We then proceeded to produce example reports, based on production data, covering metrics such as :-
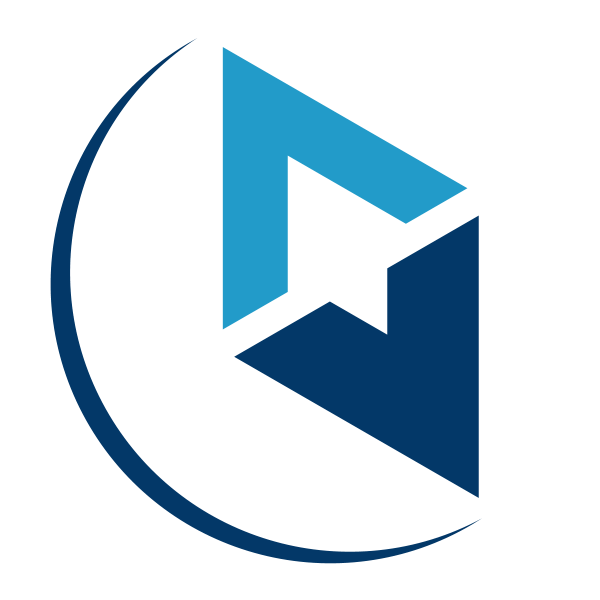
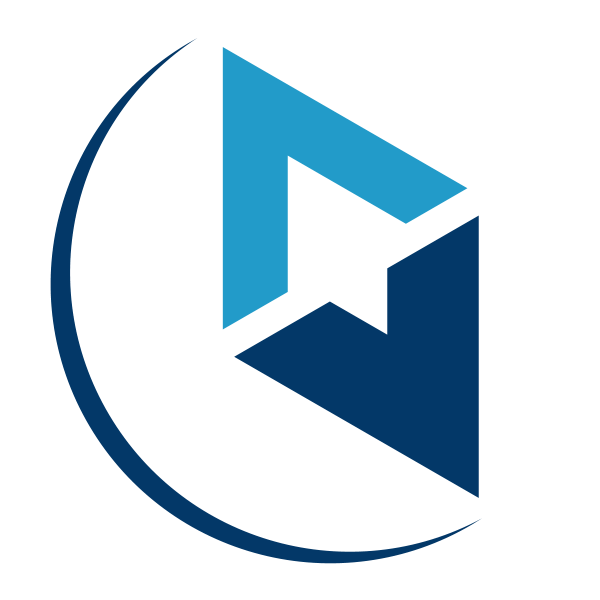
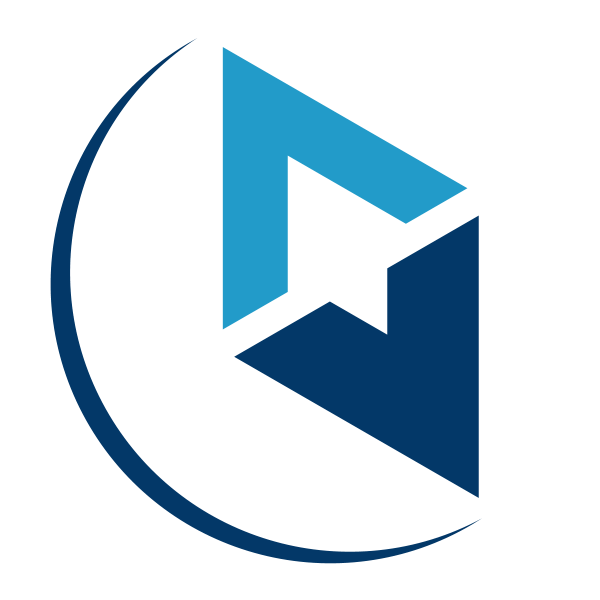
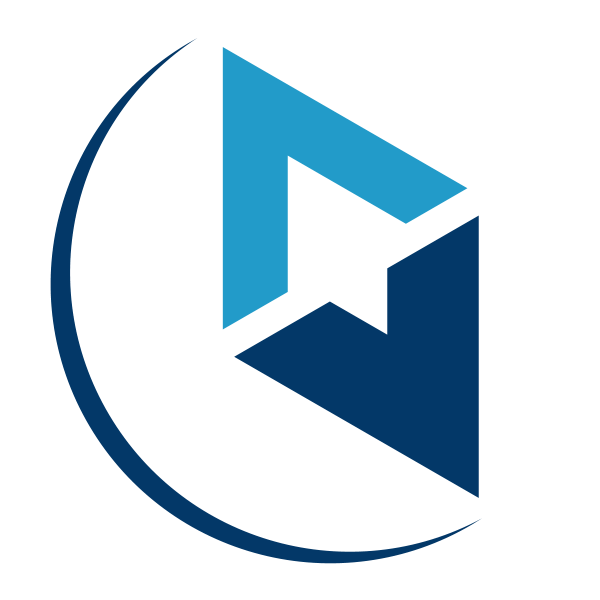
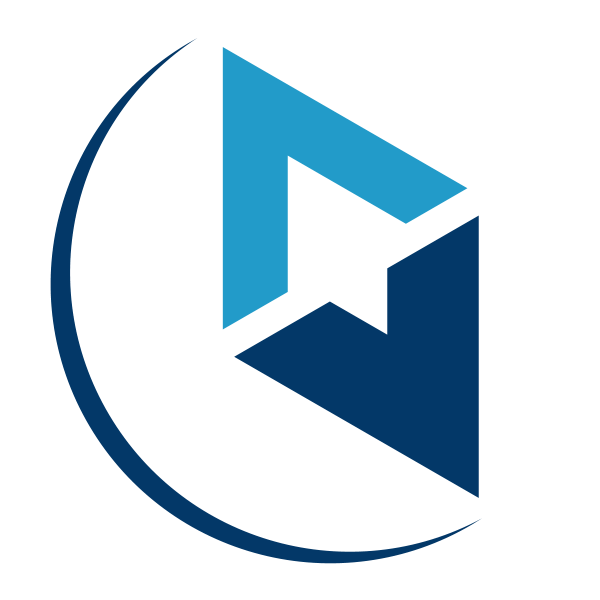
Some of the reporting needs involved minor process changes, which we managed the implementation of during the project.
The approved reports are automated within the client’s IT department.
In addition, the client has added the data extraction originally used to produce the reports, to their data warehouse. They can link this to data in their other systems (for example an equipment supervision system) and are able to produce reports and KPIs covering the entire service lifecycle – “Events” through “Incidents”, “Change Management”, “Repair”, “MTBF”.
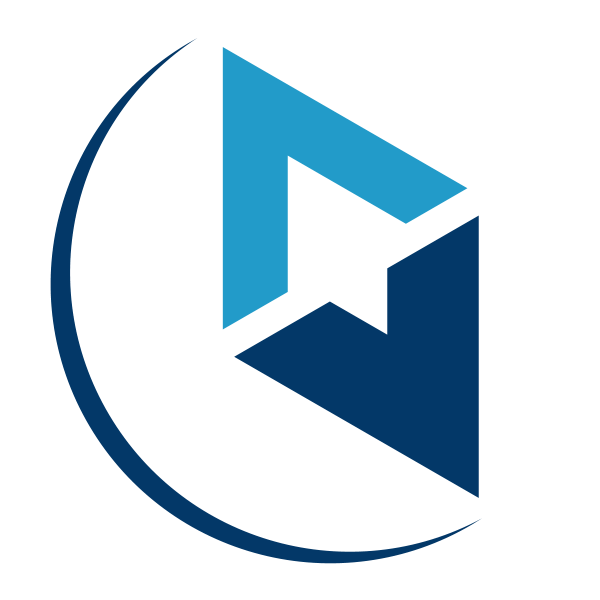

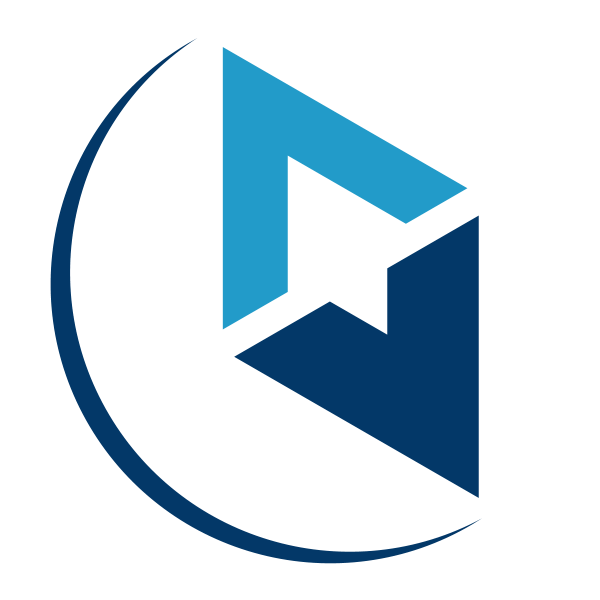





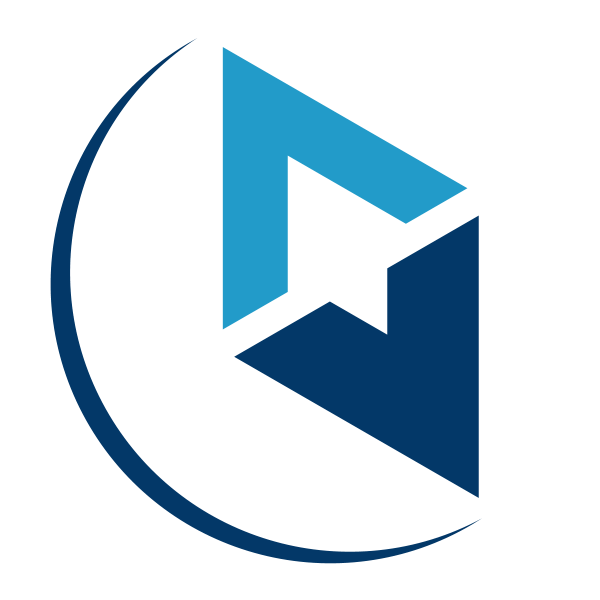
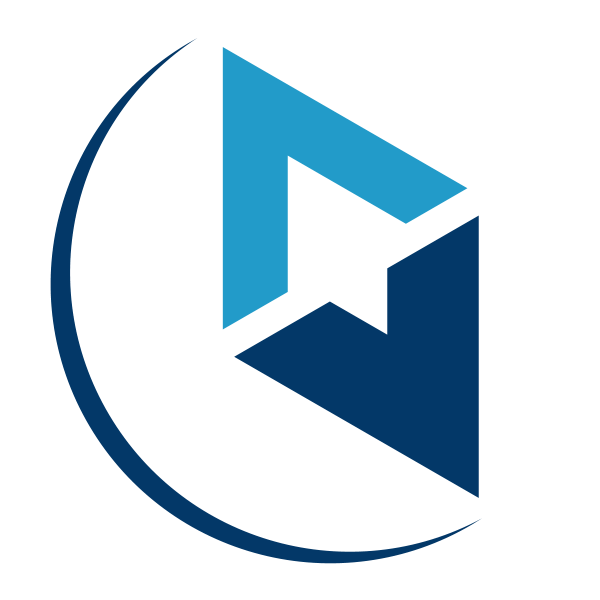
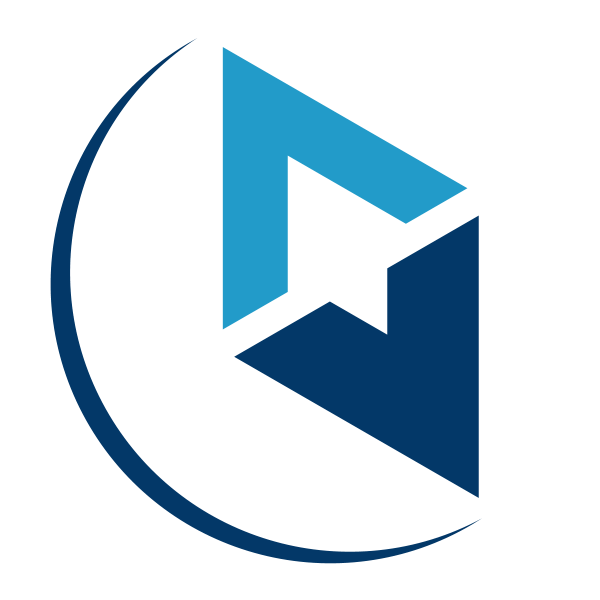